Kolfiber – dags att flyga nu?
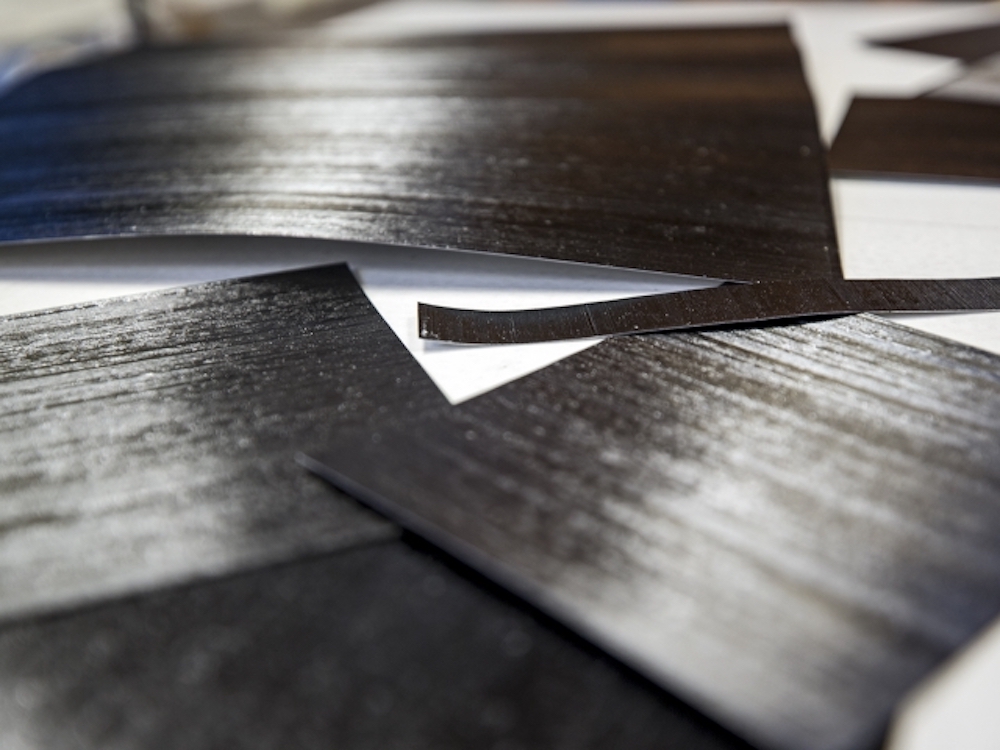
Bilbranschen har pratat om det i 20 år. Men den superlätta kolfiberbilen lyfte aldrig. Nu står ett genombrott för dörren. Skärpta utsläppskrav tvingar bilindustrin att tänka nytt.
– Det är nu det ska hända. Jag har väntat på det här sedan 1999.
Forskare Malin Åkermo berättar om ett nytt forskningsprojekt tillsammans med flera storföretag i fordonsbranschen, som vill massproducera bilkarosser i kolfiber. Det är den första stora satsningen i Sverige. Äntligen.
– Vi har sett det hända utomlands och känt oss bedrövade över att fordonsindustrin hittills inte haft något svenskt alternativ. Så detta är viktigt!
Redan i sin avhandling från 1999 visade Malin Åkermo att det fungerar. Redan då väntades kolfiber slå ut plåt som karossmaterial och i andra bildelar. Men det hela kom av sig. Plåt var fortsatt billigast och bilbranschen ändrar sig bara om den måste.
Så häromåret tog tyska premiumbiltillverkaren BMW ett tekniksprång med sin i3, en elbil i kolfiber. Plötsligt måste resten av branschen.
– BMW har gjort något alla andra måste förhålla sig till. Alla andra är tvåa på bollen. Men det kan vara bra att vara tvåa. Då kan man göra saker ännu bättre, säger Malin Åkermo.
Vi ses i labbet för farkost och flyg där Malin Åkermo jobbar. Vi står bland presenningar, dragskåp och i hörnet står en rullstol i kolfiber som är utvecklad på plats. Rösterna ekar i den stora hallen.
Malin Åkermo är en av landets ledande forskare om kompositmaterial, av vilka kolfiber är ett. Kajaker, cyklar och flygplan tillverkas redan i detta lätta material. Och 2020 kommer nya EU-regler om minskade utsläpp för fordon.
– Alla vet att vikten måste ner. En fjärdedel av utsläppen kommer från vikten, säger Malin Åkermo.
Och kolfiber är inte bara lätt, det är starkt och formbart. Och rostar inte. Fråga flygplanstillverkaren Boeing vars Airbus till hälften består av kolfiber i sin bärande vikt.
Men kolfiber är samtidigt dyrt och beter sig inte som plåt. Det kräver andra fabriker och annat slags robotik.
– Plåt vet ju konstruktörerna vad de ska göra med. Man pressar del för del. Men med kolfiber måste man göra allt annorlunda redan från början, säger Malin Åkermo.
Vi går genom labbet. Hon visar några ark av kolfiber som påminner om tapetvåder. Men hon undviker att lägga händerna på eftersom epoxyplasten, bindemedlet, fräter. Lukten från ohärdad plast är frän.
Varje tapetvåd är 0,13 millimeter tjock. Det är starkt och styvt i en riktning - åtta gånger starkare än stål - men skört i den andra riktningen. För att uppnå hållfasthet läggs tapetvåderna, impregnerade i epoxy, på varandra i olika riktningar. Det är lite som att tapetsera väggar. Man måste mönsterpassa, förklarar Malin Åkermo.
Det hela kompliceras av att väggarna som ska tapetseras inte är plana. En flygplansvinge och en bilkaross är böjd. Vi talar här ett om ett manuellt hantverk som inte lämpar sig för industrins krav.
Det tar två personers arbete under två veckor för att lägga kolfibervåder till en flygplansvinge med denna hantverksmässiga teknik. Det går möjligen när man producerar flygplan i mycket små serier men det lämpar sig inte i en automatiserad tillverkning av bilar.
Alternativet, att arbeta med torr kolfiber, kan också vara besvärligt.
– Kolfiber kan ändra egenskaper om det vrids eller om man lägger det fel. Det gäller särskilt när det är torrt. Mycket av automationen kring kolfiber handlar om att lyfta och placera det på rätt sätt, säger Malin Åkermo.
Starkt men svårberäkneligt alltså. Här ser vi en del av problemet.
– Ska man få det att fungera med serietillverkning av hundratusentals bilar måste man bygga om fabrikerna, säger hon.
När BMW bröt kolfiber-vallen gjorde man just så. Man byggde en helt ny fabrik. Plus att BMW köpte en egen kolfiberfabrik i USA för att säkra tillgången till materialet. När alla andra följer efter kan det bli brist, resonerade biltillverkaren från Bayern.
BMW tänkte utanför boxen för sin i-serie, menar Malin Åkermo. Men satsningen var så kontroversiell att BMW länge höll allt hemligt, även inom den egna organisationen.
Det BMW gör är att lägga kolfibern i en form och så gjuts hela karossen i ett stycke. Karossen blir så lätt att en person kan lyfta den utan besvär.
Men exakt hur det går till förtäljer inte videoklippen på Youtube. Inte heller de journalister eller gästforskare som besökt fabriken får veta hur BMW ställer in maskinerna eller under vilka temperaturer de arbetar.
– Det är sådana inställningar som är avgörande för om det ska vara ekonomiskt lönsamt. Det berättar de inte, även om de annars kan vara rätt öppna. Jag är övertygad om att det går att göra saker bättre än vad BMW har kommit fram till idag, säger Malin Åkermo.
Hon anar att det blir en del spill i BMW-fabriken. När de mönsterpassar måste de klippa bort stuvbitar som blir över.
Fler tekniksprång står för dörren. Kolfiber leder energi, ungefär som ett batteri. Nu laborerar forskare på KTH med att göra karossen, balkarna och andra bärande delar av bilen – till just ett batteri.
Om elbilen inte bara är bil utan samtidigt sitt eget batteri kan körsträckan, räckvidden, öka radikalt. Det kallas för strukturella batterier och forskningen involverar kemiskolan på KTH och en rad andra lärosäten.
– Det är ett jättehäftigt projekt som mina kollegor driver och som folk blir glada av att prata om. En massa företag och lärosäten är med. Flygindustrin är också intresserad. Airbus vill ha elektrifierade flygplan, säger Malin Åkermo.
Bakom ett grått tygskynke och en presenning står labbets hemligaste pjäs: en vävstol. Den får vi inte se. Vävstolen väver trådar av kolfiber, inte bara längs med utan åt alla håll. Vi har precis lärt oss att kolfiber är styvt, men bara i en riktning och för att uppnå hållfasthet måste kolfibertrådarna löpa åt alla håll.
– Man kan väva alla sorters balkar här. I-balkar, pi-balkar och balkar som är breda i början men som sedan smalnar av, egentligen vad du vill, säger Malin Åkermo.
Men hur är det med miljövänligheten? Lukten av klister förföljer oss i labbet. Kolfiber utvinns oftast ur olja, som måste bearbetas i en rad energikrävande processer och blandas med olika plaster. Försök pågår att använda smältbar termoplast som går att återanvända, men än så länge är det inte förstahandsvalet. Fast det går att göra kolfiber av trä. Lignin, en restprodukt från trä.
Redan på 1990-talet byggde Volvo en bil i kolfiber, Luciabilen, i ett exemplar. Men projektet lades ner när Ford köpte företaget. Så när ser vi den första serietillverkade svenskbyggda bilen i kolfiber?
Malin Åkermo värjer sig för frågan.
– Alla är så fixerade vid årtal. Det är nog en gradvis utveckling och det är fråga om hur mycket av bilen ska vara i komposit. I flyget är 50 procent av den bärande vikten kompositmaterial. Om det blir samma i bilen, det får vi se, säger Malin Åkermo.
FAKTA
Malin Åkermo
Ålder: 47
Aktuell: Sveriges ledande forskare om kolfiber.
Disputerade: 1999 med en avhandling om kompositmaterial.
Kör själv: Helst cykel eller åker kommunalt.
Okänd talang: Utbildad längdskidinstruktör.
Kolfiber
-Består av fiberbuntar av kol, som binds samman med ohärdad plast.
-Åtta gånger starkare än plåt per viktenhet men minst tio gånger så dyrt.
-Väger avsevärt mindre än glasfiber.
-Bildelar kan gjutas i ett stycke.
-Rostar inte.
Text Thomas Heldmark
Foto Håkan Lindgren
KTH Magazine 12 JANUARI, 2017