Research into enhanced track and switch and crossing system 2 (IN2TRACK-2) (RV36)
Project Coordinator - Network Rail
Project Leader at KTH - Mats Berg (WP3)
Scientists at KTH - Rohan Kulkarni, Alireza Qazizadeh, Saeed Hossein Nia
Sources of Funding - Trafikverket and European Commission (Horizon 2020)
In WP3 Optimised track system, KTH is working on Task 3.5 Wheel-rail interaction, more precisely on two topics: Investigate and control the hunting motions on track and understanding and mitigating curve squeal.
Investigate and control the hunting motions on track
Vehicle hunting motion is a classical issue in vehicle-track dynamic interaction. This periodic (sinusoidal) lateral motion is a safety concern and can also cause passenger discomfort. Typically, this running instability appears at fairly high vehicle speed and on straight track or in large-radius curves.
The main cause could be poor vehicle yaw dampers or too soft primary suspension. But the actual wheel-rail geometry match and track gauge are also key quantities. A key geometric quantity for the wheel-rail (wheelset-track) interface is the equivalent conicity, cf. EN 15302. The wheel-rail pair is categorised based on the equivalent conicity corresponding to 3 mm lateral wheelset displacement. Usually, this conicity should be kept low to reduce the risk of hunting motion. However, having fairly-low equivalent conicity is not sufficient to avoid running instability, as this instability of the vehicle also depends on the equivalent conicity function with lateral wheelset displacement. Therefore, a question has arisen if there are other parameters at the wheel-rail interface that play a decisive role for the running stability. Polach proposed a Nonlinearity Parameter (NP) to quantify the nonlinearity of equivalent conicity function. The objective of the present work is to investigate, through simulations, the effect of NP on running instability and to suggest further vehicle and track actions (limit values etc) to reduce the risk of vehicle hunting motion. The conclusions should state to what extent equivalent conicity should/could be accompanied by other geometric parameters, like NP, to better explain and mitigate running instability.
Understanding and mitigating curve squeal
In the wheel-rail rolling contact there is always some degree of sliding motion in the contact patch, both laterally and longitudinally. At traction (acceleration) and braking (retardation) the sliding motion is mainly longitudinal whereas in curve negotiation also the lateral sliding motion can be substantial. Curve negotiation, especially in tight curves, can cause excessive wheel and rail damage but also noise. In particular, squeal noise causes human annoyance. Squeal noise often occurs at the leading inner wheel of a bogie or two-axle vehicle. It can also occur at the flange of the outer wheel but less common. Squeal noise is associated with the falling part of the creep curve in which the friction value drops at higher creepages and the creep forces drop consequently. This causes instability in the system which eventually leads to stick-slip motion and squeal noise. A key system design and maintenance action is therefore to reduce the sliding motion in the contact patches during curve negotiation.
The objective of this work is to investigate, through simulations, system parameters that are closely related to the sliding motion and the associated curve squeal as well as mitigations of the squeal noise. In addition to the curve radius, wheel and rail profiles, wheel-rail friction and bogie steering ability are key parameters. The study will present numerical results along with design and maintenance actions to reduce the occurrence and level of curve squeal noise.
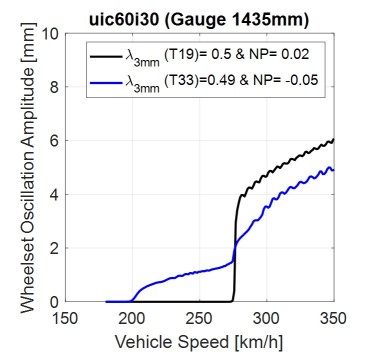
Z. Liu, " Conceptual exploration of power peak shaving by smart train operation in rail freight transport," Proceedings of the Institution of mechanical engineers. Part F, journal of rail and rapid transit, 2021.