Work Plan
The work to be accomplished in SUNRISE is partitioned into five work packages. Below, a brief description of each work package is given, together with a list of associated tasks.
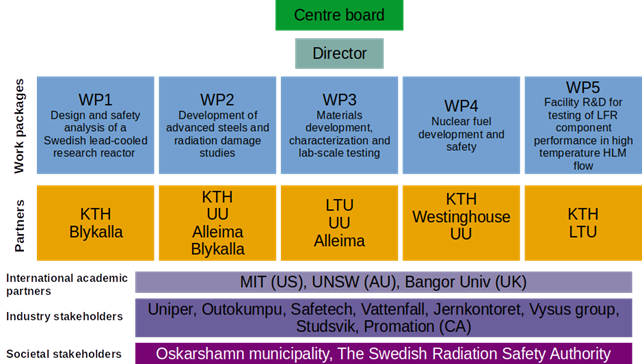
WP1: Design and safety analysis of a lead-cooled research reactor
Here, the design and safety analyis of a lead-cooled research and demonstration reactor intended to be located in Oskarshamn is carried out. The goal is to, with the support of external organisations, complete a PSAR (Preliminary Safety Analysis Report) of the reactor that may be submitted to the Swedish Radiation Safety Authority (SSM) as part of an application to build such a reactor, if funding from other sources is obtained.
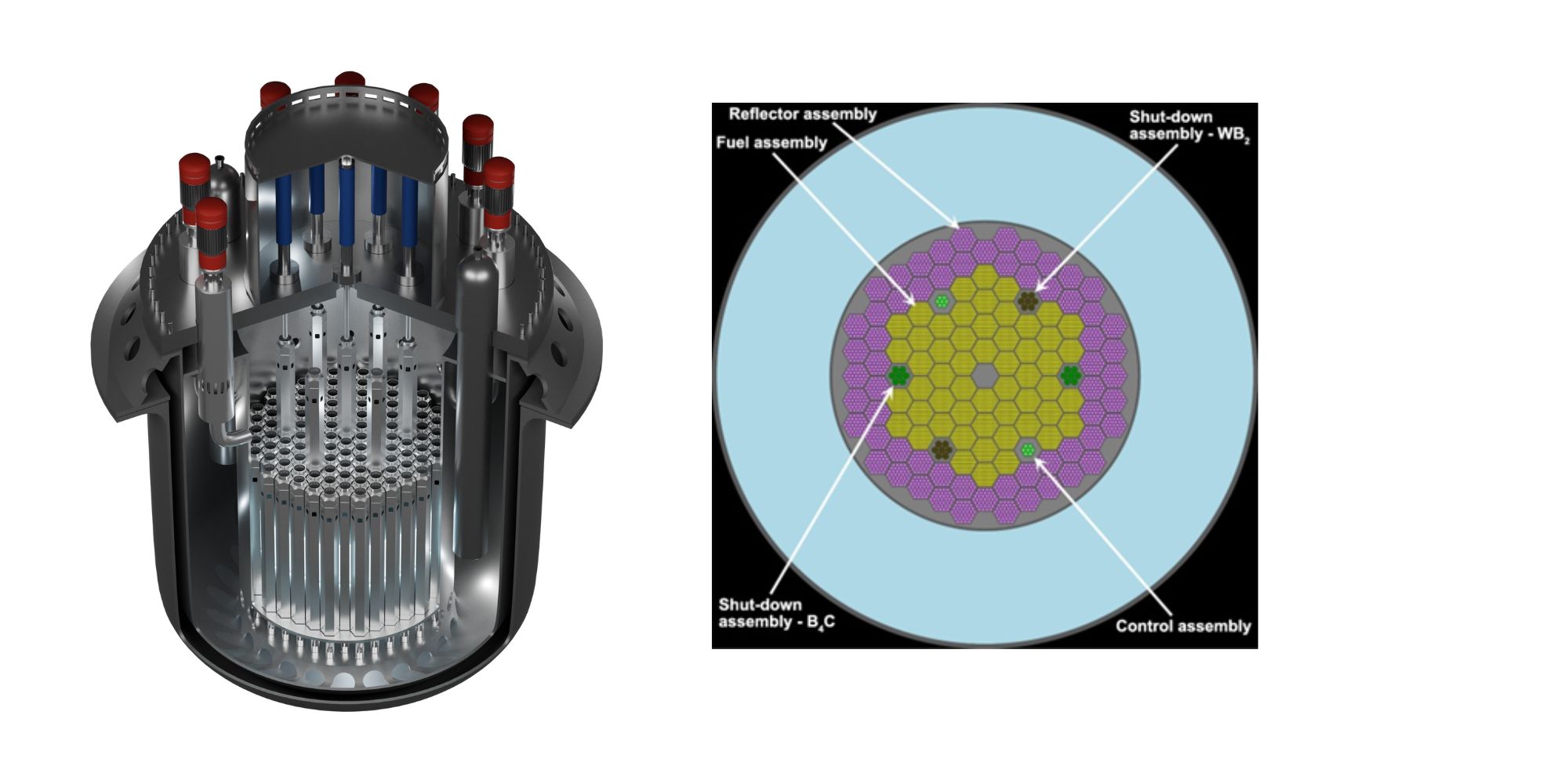
WP2: Development and modelling of advanced steels
In this work package, alumina forming steels and materials for pump impellers will be optimised, with support of thermodynamical modelling. Test samples and component prototypes are manufactured for mechanical, erosion and irradiation tests. Modelling of irradiation performance, embrittlement and interaction between lead and aluminium oxide is carried out using ab initio methods and multi-scale approaches.
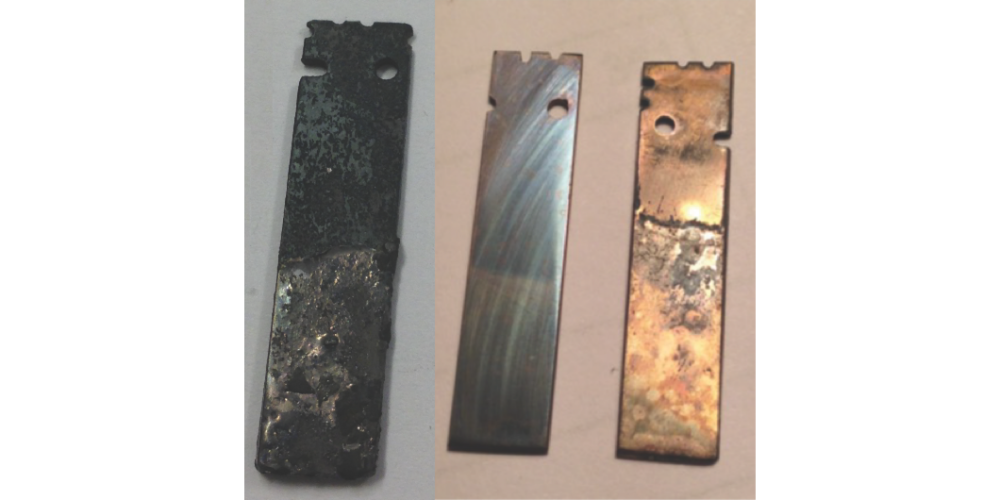
WP3: Development and testing of novel materials, coatings and manufacturing techniques
In WP3, novel coatings and coating techniques will be developed for protection of components exposed to lead. Simulated fission product nitride powders are produced for manufacture of uranium nitride simfuel in WP4. Fretting tests of alumina forming steels will be performed in a liquid lead environment. Laser welding test of alumina forming steel overlays on SS316 and 15-15Ti tubes will be conducted.
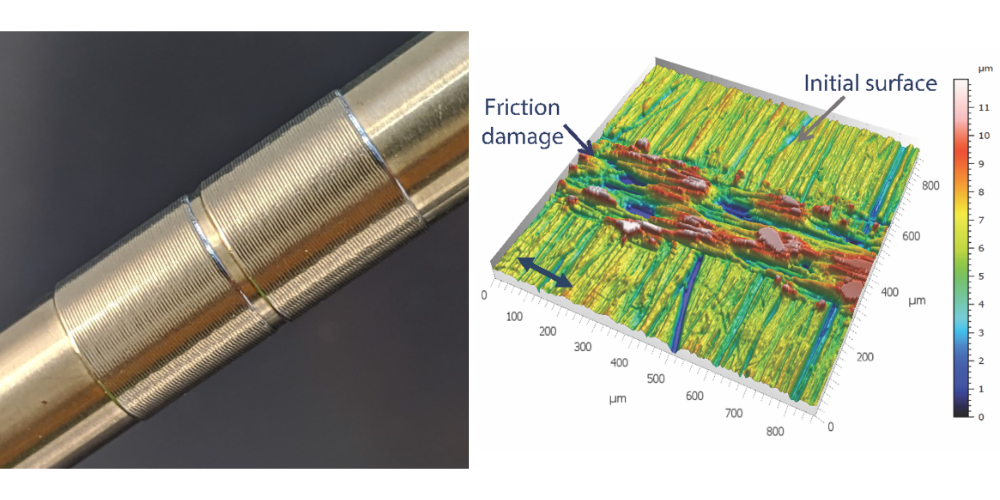
WP4: Nuclear fuel development
Here, uranium nitride fuel pellets incorporating simulated fission products will be manufactured using spark plasma sintering techniques. A range of porosities will be produced in order to mimic the effect of bubble formation. The fission products will be introduced using a variation of methods, including such developed in WP3. The degradation of fuel performance with burn-up will be assessed by measurement of heat capacity, thermal diffusivity and thermal expansion of manufactured simfuel samples.
Fuel-cladding and fuel-coolant interdiffusion experiments are carried out to determine the impact of fission products, and rod-leak tests will be conducted to assess the performance under accident conditions.
Furthermore, a thermodynamic assessment of fuel-cladding-coolant systems will be made, leading to the establishment of a thermodynamic database.
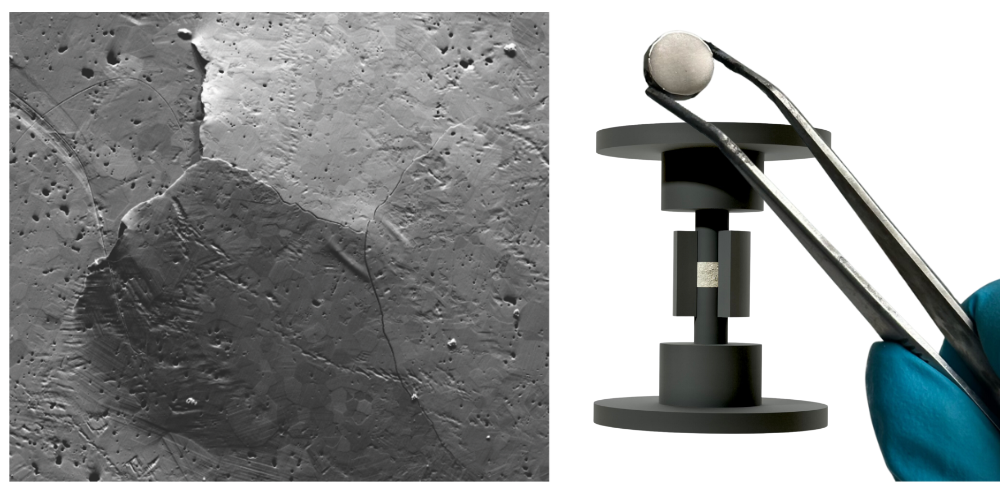
WP5: Experimental testing of LFR components
In this work package, experimental test rigs will be designed, built and used for testing and qualification of components for the research reactor designed in WP1. An erosion rig will be used for qualification of pump impellers as well as fuel cladding and steam generator tubes in prototypic lead flow regimes at temperatures up to 750 degrees C. Separate effect tests will be carried out in a smaller scale facility. Mockups using transparent liquids will be used for validation of models predicting turbulent flow characteristics in facilities using liquid lead.
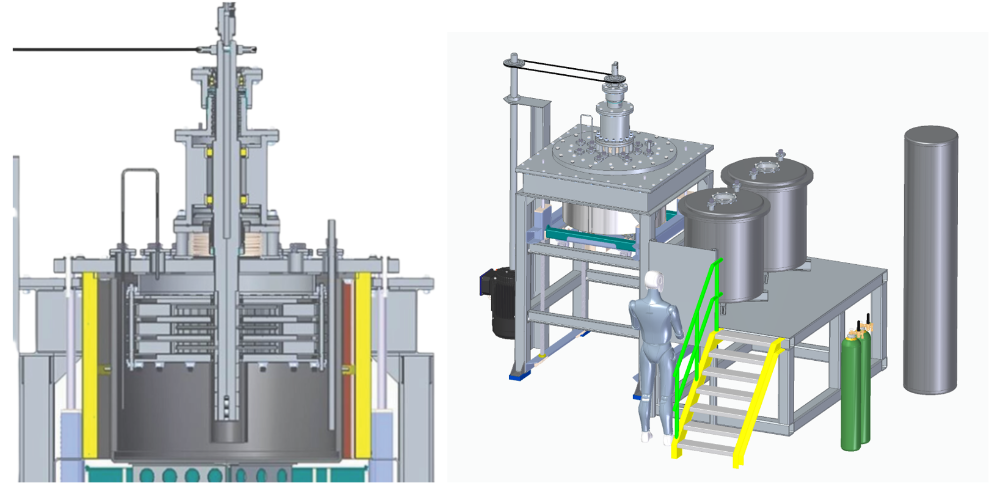