Repam drives innovation in metal powder manufacturing
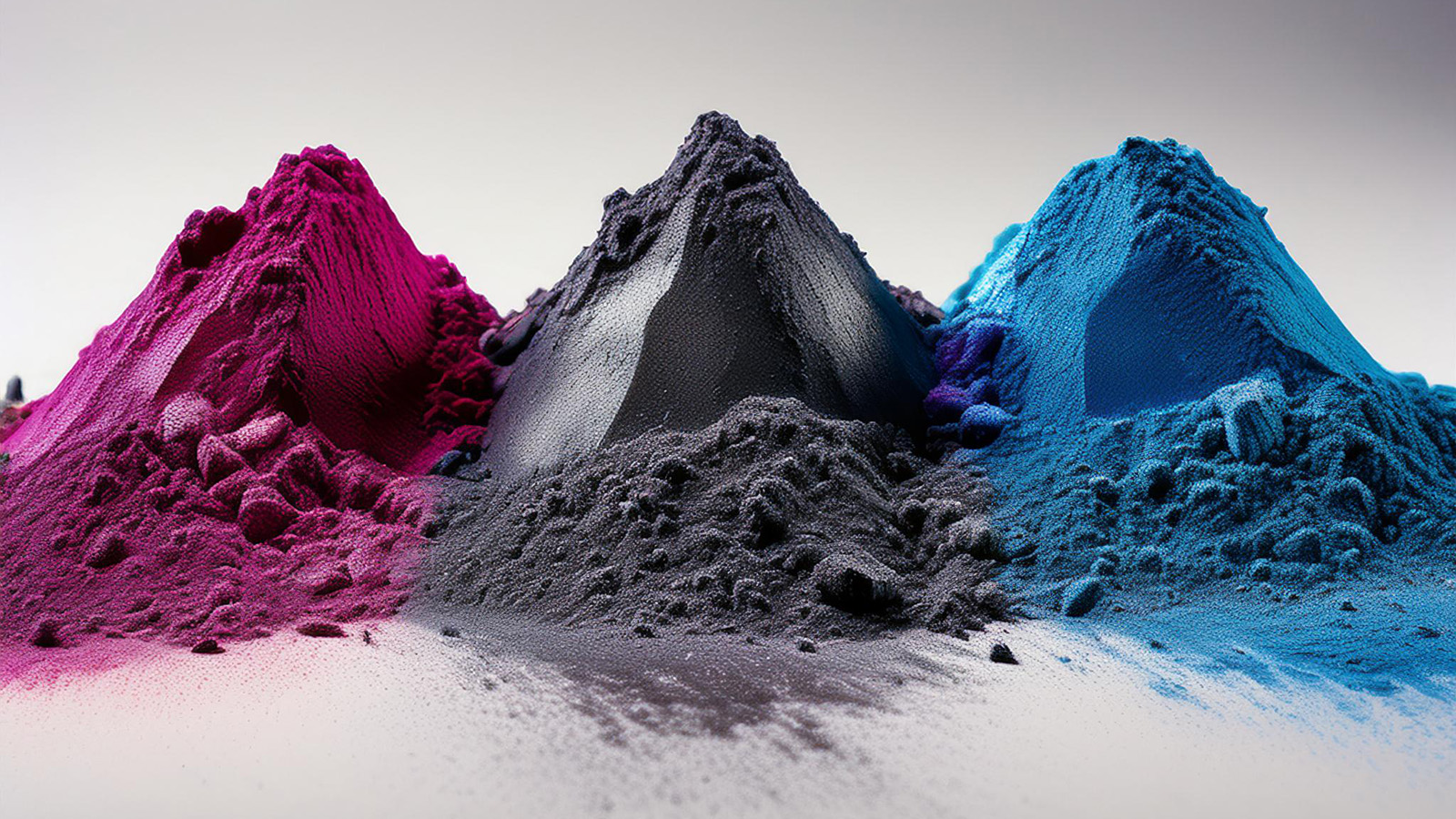
Innovative applications of new technology are ways to meet the growing demands for material performance in additive manufacturing. In a newly launched project, KTH is collaborating with research groups from across Sweden and leading European industrial companies to develop sustainable and efficient methods for powder production.
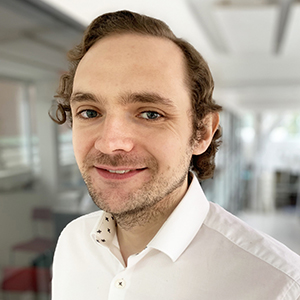
REPAM is a newly launched EU project focusing on different methods to reduce the amount of material and energy required for the production of metal powders for additive manufacturing. The methods for new production, reuse, and recycling are led by three different project teams and complement each other.
Chris Hulme Smith is leading the research on one of the sub-projects together with his colleagues Greta Lindwall and Mohammad Hoseini Athar.
“Additive manufacturing is a very flexible production method with many advantages for engineers and designers, but as a materials expert, one can see the challenges, and those are what we are trying to address in the project,” he says.
New production with gas atomisation
KTH is leading the development of new processes for gas atomisation – the most commonly used method for producing powder for additive manufacturing from scratch. Chris explains that the technology has existed for decades, but additive manufacturing has changed the size requirements of the end users. At the same time, he describes gas atomisation as a chaotic and random process, where there is currently a lack of sufficiently effective methods to control the size of the powder particles being produced:
”We start with liquid metal, which is cooled rapidly by several hundred degrees, causing the particles that will become grains to fly in all directions at speeds of many metres per second. The difficulty in measuring and adjusting during the process results in a very broad size distribution. Currently, only 30–40 percent of the original raw material produces usable metal powder for 3D printing, while the rest ends up in the wrong sizes.”
According to Chris, the hope is to achieve a 30 percent increase in the amount of usable powder by employing new measurement methods, including optical techniques that are currently used in completely different fields.
“That is really the big innovation, to combine gas atomisation with these sensor techniques. We will be able to measure and adjust the process in real-time. We will also gain information about what affects the process, including size, speed, and temperatures,” he says.
Reuse
Another method being studied in the project is the reuse of leftover powder. According to Chris, this could be more cost-effective than producing new powder, but it also presents its own challenges.
”Powder that is used in additive manufacturing processes but hasn’t formed components tends to clump together. Additionally, the surface of the powder can be affected and deteriorate after a while,” he explains.
The company Graphmatec in Uppsala is leading the development of processes to restore performance in recycled powder. They are also investigating whether damaged surface layers can be repaired by coating them with graphene.
Recycling
A problem with metal recycling is that the surface layers of scrap components may be contaminated by materials they have come into contact with. Luleå University together with a german recycling company are testing a laser based technique that previously has been used to remove painted surfaces. The contaminated layer is removed, allowing the rest of the component to be reused.
Chris says that this technique can be used to break down the entire scrap component and recover the powder directly within the recycling process, thereby also addressing a storage problem:
”Previously, for practical reasons, it has been necessary to create recycled material from various metal alloys, simply because the large amount of material has made more detailed material categorisation impossible. This can mean that the most valuable elements are diluted, reducing their effectiveness.”
Future Application
Even today, these methods have many stakeholders, including powder manufacturers, recycling companies, and manufacturing firms across the entire value chain. The future users could be many more.
”We are working with additive manufacturing in this project, and the end users want powder for aircraft components, cars, and other products. However, once the techniques are in place, they could have much broader applications across various manufacturing processes,” says Chris.
Text: Alexandra von Kern
The article was originally published in Swedish in the trade magazine Bergsmannen with news from the steel, metal, foundry, mining, and rock material industries.