Paper waste makes greener steel
Osmet 3.0 shows the way for large-scale collaboration
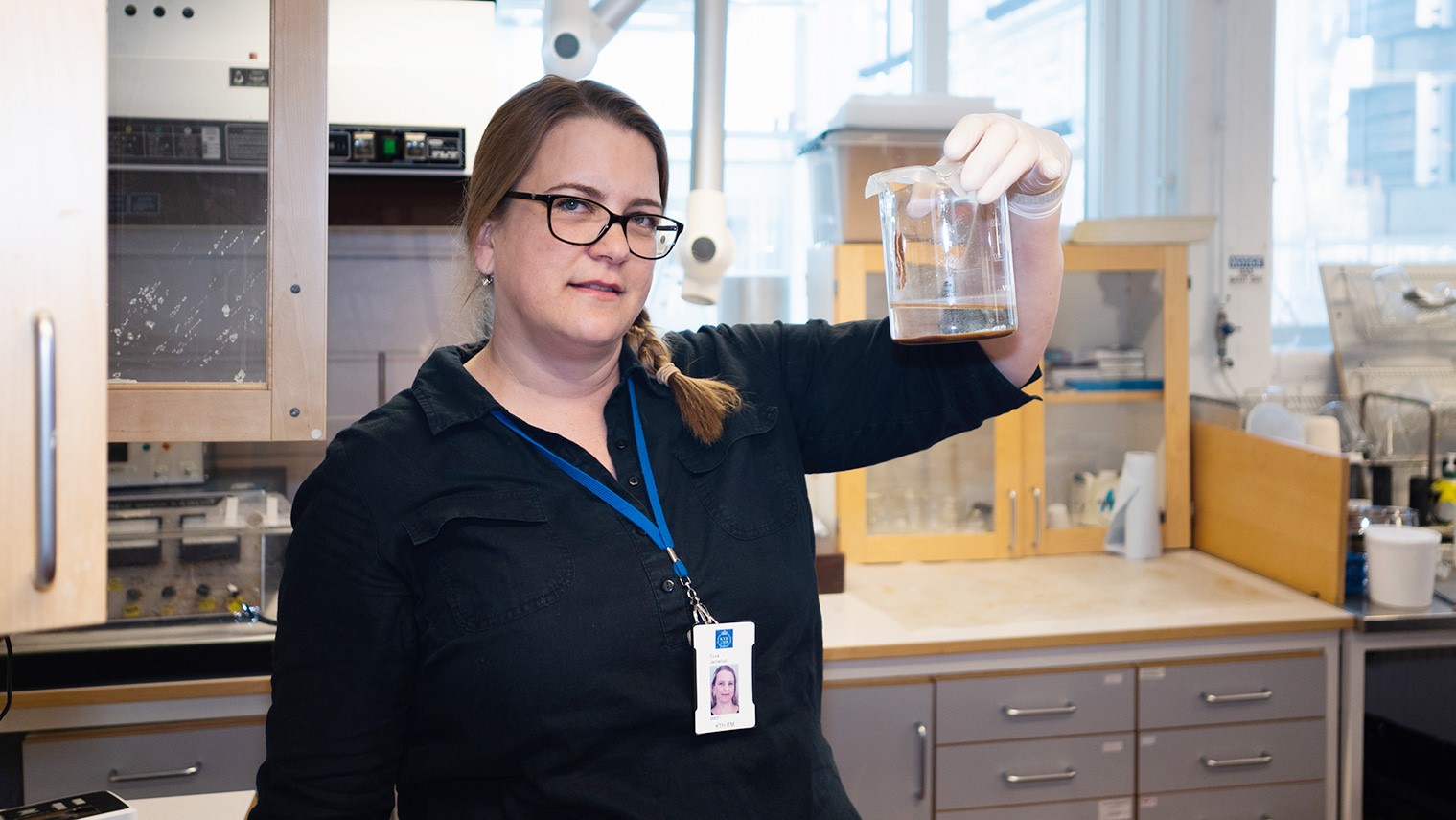
If the ideal sustainability project saves both the environment and money, and at the same time develops a research area, Osmet might be just that. Two of Sweden's largest basic industries join forces in an industrial and environmental win-win, where one's waste is processed into the other one’s raw materials. A project now entering its third step and made possible by, among others, researchers at KTH.
Osmet is based on the possibility of using processed waste from the pulp and paper industry as raw material in various steelmaking processes. Tova Jarnerud , Doctoral Student in Materials Science at KTH, does research for the project.

”The pulp and paper industries generate large amounts of coal and calcareous waste. Today, much of this waste ends up in landfills, and at the same time new raw material is mined for use in various metallurgical processes. Seeing the waste products as a resource instead of a problem gives us new opportunities.”
According to Tova Jarnerud, the benefits are many if the project reaches its goals. The steel industry can reduce its dependence on fossil fuels and natural materials. At the same time, the pulp and paper industry can reduce the amount of land needed for landfills – and not least the greenhouse gases that these generate. Landfills also involve large costs for the industry.
More sustainable alternatives
”In the project's previous steps, we have shown that we can successfully upgrade coal and calcareous waste from the pulp and paper industry, and use it as raw materials in different stages of the steel manufacturing process”, says Tova Jarnerud.

In laboratory experiments the research team have been able to replace 100 percent of the primary lime, used to purify acidic waste water in steel mills, with recycled materials. And in pilot-scale experiments, up to 50 percent of the slag-forming lime – an important component that binds unwanted substances in the steel – could be replaced by recycled material.
”We have also done industrial experiments with organic sludge in briquettes for the blast furnace. In the experiments, no negative effects were noted regarding production speed or quality of the pig iron, but the proportion of organic sludge was modest and further tests are needed.”
Focus on the steelmaking processes of the future
Osmet is now entering its third phase, where experiences from previous steps will be tested on a larger scale and industrialized.
”For example, we need to find out how far the material can be transported before the environmental impact and cost overcome the benefits, and we need to map out where the producers of useful material and the potential users are”, says Tova Jarnerud.
The prospect is that enough material can be recycled to motivate large-scale industrial applications in the future. According to Tova Jarnerud, there may also be more discoveries along the way:
”I hope that we find more new uses for the recycled materials, and new smart ways to reuse other residual products as well. In the third step, we have new partner companies with us that can contribute to innovative solutions.”
Text: Alexandra von Kern